Цемент, загалом, клейкі речовини всіх видів, але, в більш вузькому сенсі, в’яжучі матеріали, що використовуються в будівництві та цивільному будівництві. Цемент – це тонко подрібнений порошок, який при змішуванні з водою перетворюється на тверду масу. Схоплювання і твердіння відбувається в результаті гідратації – хімічної взаємодії цементних сполук з водою, в результаті якої утворюються субмікроскопічні кристали або гелеподібний матеріал з великою площею поверхні. Через свої гідратаційні властивості будівельні цементи, які схоплюються і тверднуть навіть під водою, часто називають гідравлічними цементами. Найважливішим з них є портландцемент.
У цій статті розглядається історичний розвиток цементу, його виготовлення із сировини, склад і властивості, а також випробування цих властивостей. Основна увага приділяється портландцементу, але також розглядаються інші види цементу, такі як шлаковмісний цемент і високоглиноземистий цемент. Будівельні цементи мають спільні хімічні складові та методи обробки з керамічними виробами, такими як цегла і плитка, абразивні матеріали та вогнетривкі матеріали. Детальний опис одного з основних застосувань цементу див. у статті Будівництво.
Застосування цементу
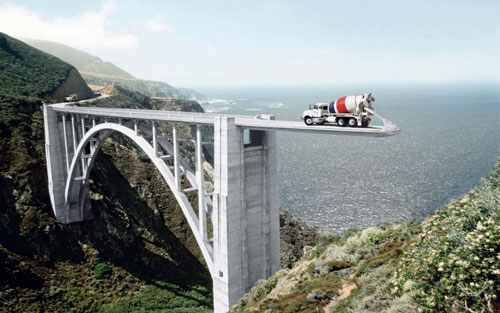
Ілюстрація: wallhere.com
Цемент може використовуватися окремо (тобто, “чисто”, як цементний розчин), але зазвичай його застосовують у складі будівельних розчинів і бетонів, в яких цемент змішується з інертним матеріалом, відомим як заповнювач. Розчин – це цемент, змішаний з піском або щебенем, розмір якого повинен бути менше приблизно 5 мм (0,2 дюйма). Бетон – це суміш цементу, піску або іншого дрібного заповнювача і грубого заповнювача, який для більшості цілей має розмір від 19 до 25 мм (від 0,75 до 1 дюйма), але грубий заповнювач може мати розмір до 150 мм (6 дюймів), коли бетон укладається у великі масиви, такі як дамби. Будівельні розчини використовуються для зв’язування цегли, блоків і каменю в стінах або для облицювання поверхонь. Бетон використовується для найрізноманітніших будівельних цілей. Суміші ґрунту і портландцементу використовуються як основа для доріг. Портландцемент також використовується у виробництві цегли, черепиці, бітумної черепиці, труб, балок, залізничних шпал і різних екструдованих виробів. Вироби виготовляються на заводах і поставляються готовими до монтажу.
Виробництво цементу надзвичайно поширене, оскільки бетон є найпоширенішим з усіх будівельних матеріалів у сучасному світі.
Історія цементу
Історія гідравлічних цементів сягає корінням у Стародавню Грецію та Рим. Використовувалися вапно та вулканічний попіл, який повільно реагував з ним у присутності води, утворюючи тверду масу. Так формувався цементуючий матеріал римських розчинів і бетонів понад 2 000 років тому, а також подальших будівельних робіт у Західній Європі. Вулканічний попіл, що видобувався поблизу сучасного міста Поццуолі, Італія, був особливо багатий на основні алюмосилікатні мінерали, що дало початок класичному пуццолановому цементу римської епохи. До сьогодні термін “пуццолан”, або “пуццолан”, відноситься або до самого цементу, або до будь-якого дрібнодисперсного алюмосилікату, який вступає в реакцію з вапном у воді, утворюючи цемент. (Термін “цемент” походить від латинського слова caementum, яке означало кам’яну крихту, яку використовували в римському будівельному розчині, а не сам в’яжучий матеріал).
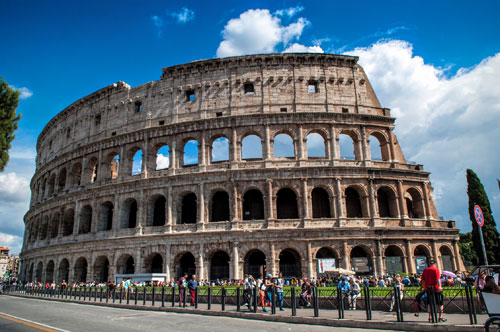
Руїни Колізею в Римі. Фото: livejournal.com
Портландцемент є наступником гідравлічного вапна, яке вперше розробив Джон Смітон у 1756 році, коли його запросили звести маяк Еддістоун біля узбережжя Плімута, графство Девон, Англія. Наступною розробкою, що відбулася близько 1800 року в Англії та Франції, був матеріал, отриманий шляхом випалювання конкрецій глинистого вапняку. Незабаром після цього в Сполучених Штатах подібний матеріал був отриманий шляхом спалювання природної речовини під назвою “цементна порода”. Ці матеріали належать до класу, відомого як природний цемент, споріднений з портландцементом, але більш легко випалюваний і не контрольований за складом.
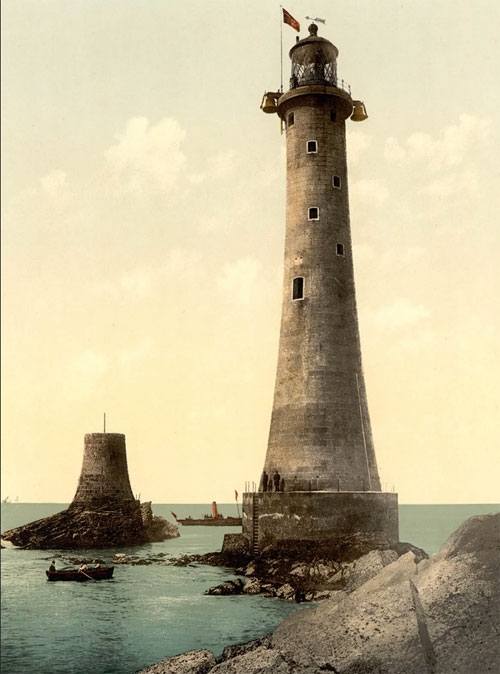
Еддістоунський маяк сера Джеймса Н. Дугласа, Плімут, Англія, фотохромний відбиток, бл. 1890-1900 років. Ліворуч – залишки маяка Джона Смітона.
Відділ естампів і фотографій, Бібліотека Конгресу США, Вашингтон, округ Колумбія
Винахід портландцементу зазвичай приписують Джозефу Аспдіну з Лідса, Йоркшир, Англія, який у 1824 році отримав патент на матеріал, виготовлений із синтетичної суміші вапняку і глини. Він назвав продукт “портландцементом” через вигадану схожість матеріалу, коли він застигає, з портландським каменем – вапняком, який використовувався для будівництва в Англії. Продукт Аспдіна, можливо, був занадто легко випалений, щоб бути справжнім портландцементом, і справжнім прототипом, можливо, був продукт, вироблений Ісааком Чарльзом Джонсоном у південно-східній Англії близько 1850 року. Виробництво портландцементу швидко поширилося в інших європейських країнах та Північній Америці. Протягом 20 століття виробництво цементу поширилося по всьому світу. До 2019 року Китай та Індія стали світовими лідерами з виробництва цементу, за ними йдуть В’єтнам, США та Єгипет.
Сировина
Склад
Портландцемент складається в основному зі сполук вапна (оксиду кальцію, CaO), змішаного з кремнеземом (діоксидом кремнію, SiO2) і глиноземом (оксидом алюмінію, Al2O3). Вапно отримують з вапняної (вапновмісної) сировини, а інші оксиди – з аргіліту (глинистої) сировини. Додаткова сировина, така як кварцовий пісок, оксид заліза (Fe2O3) і гідратований алюміній, що містить боксити, Al(OH)3, може використовуватися в менших кількостях для отримання бажаного складу.
Найпоширенішою вапняною сировиною є вапняк і крейда, але також використовуються й інші, наприклад, корали або відкладення черепашок. Глини, сланці, сланці та глинисті грязі є поширеною кам’янистою сировиною. Мергель, компактна вапняна глина, і цементна порода містять як вапняні, так і кременисті компоненти в пропорціях, які іноді наближаються до складу цементу. Іншою сировиною є доменний шлак, який складається переважно з вапна, кремнезему та глинозему і змішується з вапняним матеріалом з високим вмістом вапна. Каолін, біла глина, яка містить мало оксиду заліза, використовується як глинистий компонент для білого портландцементу. Промислові відходи, такі як летюча зола і карбонат кальцію з хімічного виробництва, є іншою можливою сировиною, але їх використання невелике в порівнянні з природними матеріалами.
Вміст магнезії (оксиду магнію, MgO) в сировині повинен бути низьким, оскільки допустима межа в портландцементі становить від 4 до 5 відсотків. Інші домішки в сировині, які повинні бути суворо обмежені, – це сполуки фтору, фосфати, оксиди і сульфіди металів, а також надмірний вміст лугів.
Ще однією важливою сировиною є гіпс, близько 5 відсотків якого додають до обпаленого цементного клінкеру під час помелу, щоб контролювати час схоплювання цементу. Портландцемент також може бути виготовлений у комбінованому процесі з сірчаною кислотою з використанням сульфату або ангідриту кальцію замість карбонату кальцію. Діоксид сірки, що утворюється в димових газах при спалюванні, перетворюється на сірчану кислоту за допомогою звичайних процесів.
Видобуток і переробка
Сировину для виробництва цементу видобувають кар’єрним способом, якщо йдеться про тверді породи, такі як вапняки, сланці та деякі сланці, за необхідності використовуючи вибухові роботи. Деякі родовища видобувають підземним способом. М’якші породи, такі як крейда і глина, можуть видобуватися безпосередньо екскаваторами.
Видобуті матеріали транспортуються до дробарки вантажівками, залізничними вагонами, конвеєрами або канатними дорогами. Вони також можуть транспортуватися у вологому стані або у вигляді пульпи по трубопроводу. У регіонах, де вапняки з достатньо високим вмістом вапна недоступні, можна використовувати певний процес збагачення. Пінна флотація видаляє надлишок кремнезему або глинозему і таким чином покращує вапняк, але це дорогий процес, і його застосовують лише тоді, коли цього не можна уникнути.
Виробництво цементу
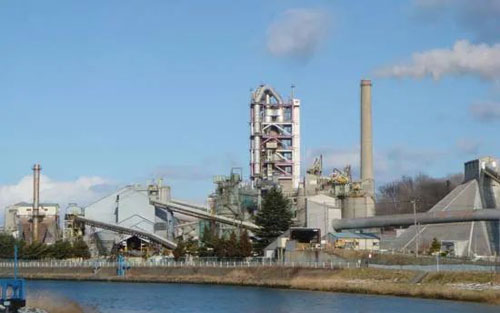
Цементний завод, Хатінохе, префектура Аоморі, Японія. Фото: britannica.com
Виробництво портландцементу складається з чотирьох етапів: (1) дроблення і подрібнення сировини, (2) змішування матеріалів у правильних пропорціях, (3) випалювання готової суміші в печі і (4) подрібнення обпаленого продукту, відомого як “клінкер”, разом з приблизно 5 відсотками гіпсу (для контролю часу схоплювання цементу). Ці три способи виробництва відомі як мокрий, сухий і напівсухий способи і називаються так, коли сировина подрібнюється мокрим способом і подається в піч у вигляді суспензії, подрібнюється сухим способом і подається у вигляді сухого порошку, або подрібнюється сухим способом, а потім зволожується до утворення вузликів, які подаються в піч.
За оцінками, близько 4-8 відсотків світових викидів вуглекислого газу (CO2) припадає на виробництво цементу, що робить його основним чинником глобального потепління. Деякі з рішень проблеми викидів парникових газів є загальними для інших секторів, наприклад, підвищення енергоефективності цементних заводів, заміна викопних видів палива на відновлювані джерела енергії, а також уловлювання та зберігання CO2, що викидається. Крім того, враховуючи, що значна частина викидів є невід’ємною частиною виробництва клінкеру, нові цементи та альтернативні рецептури, які зменшують потребу в клінкері, є важливою сферою уваги.
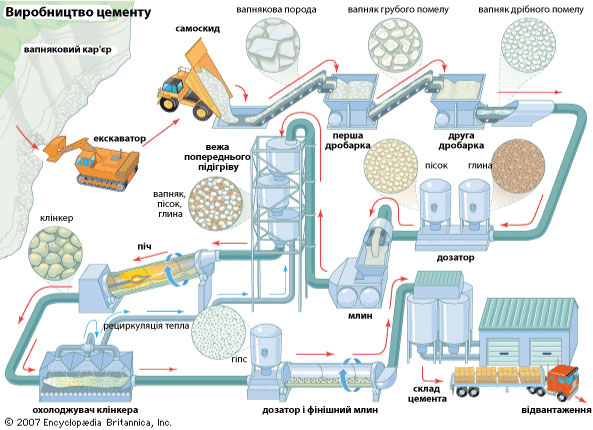
Процес виробництва цементу, від дроблення і подрібнення сировини, через випалювання подрібнених і змішаних інгредієнтів, до остаточного охолодження і зберігання готового продукту. Ілюстрація: Encyclopædia Britannica, Inc.
Дроблення та подрібнення
Усі матеріали, крім м’яких, спочатку дроблять, часто в два етапи, а потім подрібнюють, як правило, в обертових, циліндричних кульових або трубних млинах із завантаженням сталевих помольних куль. Таке подрібнення здійснюється мокрим або сухим способом, залежно від використовуваного процесу, але для сухого подрібнення сировину спочатку може знадобитися висушити в циліндричних, обертових сушарках.
М’які матеріали подрібнюються шляхом інтенсивного перемішування з водою в промивних млинах, утворюючи дрібнодисперсну суспензію, яку пропускають через сита для видалення негабаритних частинок.
Змішування
Перше наближення до хімічного складу, необхідного для конкретного цементу, отримують шляхом вибіркового видобутку і контролю сировини, що подається на дробильно-розмелювальну установку. Більш точний контроль досягається шляхом відбору матеріалу з двох або більше партій, що містять сировинні суміші з дещо різним складом. При сухому способі ці суміші зберігаються в силосах; при мокрому способі використовуються шламові резервуари. Ретельне перемішування сухих матеріалів у силосах забезпечується перемішуванням та інтенсивною циркуляцією, що викликається стисненим повітрям. При мокрому способі перемішування відбувається за допомогою механічних засобів або стисненого повітря, або і того, і іншого. Суспензію, яка містить 35-45% води, іноді фільтрують, зменшуючи вміст води до 20-30%, а потім фільтрувальний осад подають у піч. Це зменшує споживання палива для спалювання.
Випалювання
Найпершими печами, в яких цемент випалювали партіями, були пляшкові печі, потім камерні печі, а потім шахтні печі безперервної дії. Шахтні печі в модернізованому вигляді все ще використовуються в деяких країнах, але домінуючим способом випалювання є обертова піч. Ці печі – довжиною до 200 метрів (660 футів) і діаметром шість метрів на заводах мокрого способу виробництва, але коротші для сухого способу – складаються зі сталевої циліндричної оболонки, футерованої вогнетривкими матеріалами. Вони повільно обертаються навколо осі, нахиленої на кілька градусів до горизонталі. Сировина, що подається з верхнього кінця, повільно рухається вниз по печі до нижнього, або обпалювального, кінця. Паливом для випалу може бути вугільний пил, нафта або природний газ, що впорскується через трубу. Температура в кінці випалу коливається від 1 350 до 1 550 °C (2 460-2 820 °F), залежно від сировини, що спалюється. У задній частині печі зазвичай встановлюється певна форма теплообмінника, щоб збільшити передачу тепла сировині, що надходить, і таким чином зменшити втрату тепла у відхідних газах. Випалений продукт виходить з печі у вигляді невеликих вузликів клінкеру. Вони потрапляють в охолоджувачі, де тепло передається повітрю, що надходить, і продукт охолоджується. Клінкер може бути негайно подрібнений на цемент або зберігатися на складах для подальшого використання.
При напівсухому способі сировина у вигляді конкрецій, що містять від 10 до 15 відсотків води, подається на рухому ланцюгову решітку перед тим, як потрапити до коротшої обертової печі. Гарячі гази, що надходять з печі, всмоктуються через сировину на колосниковій решітці, попередньо нагріваючи її.
Викиди пилу з цементних печей можуть бути серйозною проблемою. У населених пунктах зазвичай і часто обов’язково встановлюють циклони, рукавні фільтри або електростатичні пиловловлювачі між виходом з печі і димовою трубою. Понад 50 відсотків викидів від виробництва цементу нерозривно пов’язані з виробництвом клінкеру і є побічним продуктом хімічної реакції, яка є рушійною силою поточного процесу. Існує потенціал для змішування клінкеру з альтернативними матеріалами, щоб зменшити потребу в самому клінкері і, таким чином, допомогти зменшити вплив процесу виробництва цементу на клімат.
Сучасні цементні заводи оснащені складними приладами для контролю процесу випалу. На деяких заводах сировина відбирається автоматично, а комп’ютер розраховує і контролює склад сировинної суміші. Продуктивність найбільших обертових печей перевищує 5 000 тонн на добу.
Перемелювання
Клінкер і необхідну кількість гіпсу подрібнюють до тонкого порошку в горизонтальних млинах, подібних до тих, що використовуються для подрібнення сировини. Матеріал може проходити безпосередньо через млин (подрібнення по відкритому контуру), або грубіший матеріал може відокремлюватися від подрібненого продукту і повертатися в млин для подальшого подрібнення (подрібнення по закритому контуру). Іноді до вихідного матеріалу додають невелику кількість помольних добавок. Для цементів, що поглинають повітря (розглянуті в наступному розділі), додавання повітропоглинаючого агента відбувається аналогічним чином.
Готовий цемент пневматичним насосом перекачується в силоси для зберігання, звідки його забирають для пакування в паперові мішки або для відвантаження в контейнерах для насипних вантажів.
Основні цементи: склад і властивості
Портландцемент
Хімічний склад
Портландцемент складається з чотирьох основних сполук: трикальцієвого силікату (3CaO • SiO2), дикальцієвого силікату (2CaO • SiO2), трикальцієвого алюмінату (3CaO • Al2O3) і тетракальцієвого алюмоферриту (4CaO • Al2O3Fe2O3). У скороченому позначенні, що відрізняється від звичайних атомних символів, ці сполуки позначаються як C3S, C2S, C3A і C4AF, де C означає оксид кальцію (вапно), S – кремнезем, A – глинозем і F – оксид заліза. Також присутні невеликі кількості нерозчиненого вапна і магнезії, луги та незначні кількості інших елементів.
Гідратація
Найважливішими гідравлічними компонентами є силікати кальцію, C2S і C3S. При змішуванні з водою силікати кальцію реагують з молекулами води, утворюючи гідрат силікату кальцію (3CaO • 2SiO2 • 3H2O) і гідроксид кальцію (Ca[OH]2). Ці сполуки мають скорочені позначення C-S-H (представлені середньою формулою C3S2H3) і CH, а реакція гідратації може бути грубо представлена наступними реакціями:
2C3S + 6H = C3S2H3 + 3CH
2C2S + 4H = C3S2H3 + CH
На початковій стадії гідратації вихідні сполуки розчиняються, причому при розчиненні їх хімічних зв’язків виділяється значна кількість тепла. Потім, з причин, які до кінця не зрозумілі, гідратація зупиняється. Цей період спокою надзвичайно важливий для укладання бетону. Без періоду спокою не було б цементовозів; заливку потрібно було б робити відразу після змішування.
Після періоду спокою (який може тривати кілька годин) цемент починає тверднути, оскільки утворюються CH і C-S-H. Це цементуючий матеріал, який зв’язує цемент і бетон разом. У процесі гідратації вода і цемент безперервно витрачаються. На щастя, продукти C-S-H і CH займають майже той самий об’єм, що й вихідні цемент і вода; об’єм приблизно зберігається, а усадка є керованою.
Хоча у наведених вище формулах C-S-H розглядається як певна стехіометрія з формулою C3S2H3, вона зовсім не утворює впорядкованої структури однорідного складу. C-S-H насправді є аморфним гелем з дуже мінливою стехіометрією. Співвідношення C до S, наприклад, може коливатися від 1:1 до 2:1, залежно від складу суміші та умов затвердіння.
Структурні властивості
Міцність, яку розвиває портландцемент, залежить від його складу і тонкості помелу. C3S в основному відповідає за міцність, що розвивається в перший тиждень твердіння, а C2S – за подальше збільшення міцності. Сполуки глинозему і заліза, які присутні в менших кількостях, мають незначний безпосередній вплив на міцність.
Затверділий цемент і бетон можуть руйнуватися під впливом деяких природних або штучних хімічних речовин. Сполука глинозему є найбільш вразливою до хімічного впливу в ґрунтах, що містять сульфатні солі, або в морській воді, в той час як сполука заліза і два силікати кальцію є більш стійкими. Гідроксид кальцію, що виділяється під час гідратації силікатів кальцію, також вразливий до впливу. Оскільки цемент виділяє тепло під час гідратації, бетон, розміщений у великих масах, як у дамбах, може спричинити підвищення температури всередині масиву на 40 °C (70 °F) вище за зовнішню температуру. Подальше охолодження може стати причиною розтріскування. Найвищу теплоту гідратації має C3A, за ним у порядку зменшення йдуть C3S, C4AF і C2S.
Типи портландцементу
П’ять типів портландцементу стандартизовані в США Американським товариством з випробувань і матеріалів (ASTM): звичайний (тип I), модифікований (тип II), високоміцний (тип III), низькотемпературний (тип IV) і сульфатостійкий (тип V). В інших країнах тип II не виділяють, а тип III називають швидкотвердіючим. Тип V відомий у деяких європейських країнах як цемент Феррарі.
Існують також різні інші спеціальні типи портландцементу. Кольорові цементи виготовляються шляхом розтирання 5-10 відсотків відповідних пігментів з білим або звичайним сірим портландцементом. Повітропоглинаючі цементи виготовляються шляхом додавання при помелі невеликої кількості, близько 0,05 відсотка, органічної речовини, яка викликає захоплення дуже дрібних бульбашок повітря в бетоні. Це підвищує стійкість бетону до замерзання-відтавання в холодному кліматі. Повітропоглинач можна також додавати як окремий інгредієнт до суміші під час виготовлення бетону.
Низьколужні цементи – це портландцементи із загальним вмістом лугів не вище 0,6 відсотка. Вони використовуються в бетоні, виготовленому з певних типів заповнювачів, які містять форму кремнезему, що реагує з лугами, викликаючи розширення, яке може зруйнувати бетон.
Кладочні цементи використовуються в основному для розчину. Вони складаються з суміші портландцементу і меленого вапняку або іншого наповнювача разом з повітровтягувальним агентом або водовідштовхувальною добавкою. Гідрофобним цементом називають портландцемент, до якого додано водовідштовхувальну добавку. Гідрофобний цемент отримують шляхом подрібнення портландцементного клінкеру з плівкоутворюючою речовиною, такою як олеїнова кислота, з метою зменшення швидкості руйнування при зберіганні цементу в несприятливих умовах.
Цементи для нафтових свердловин використовуються для цементування при бурінні нафтових свердловин, де вони піддаються впливу високих температур і тисків. Зазвичай вони складаються з портландцементу або пуцоланового цементу зі спеціальними органічними сповільнювачами, які запобігають швидкому схопленню цементу.
Шлакові цементи
Гранульований шлак, отриманий шляхом швидкого охолодження відповідних розплавлених шлаків доменних печей, є основою іншої групи будівельних цементів. Суміш портландцементу і гранульованого шлаку, що містить до 65% шлаку, відома в англомовних країнах як портландцемент для доменних печей (шлакопортландцемент). Німецькі Eisenportlandzement і Hochofenzement містять до 40 і 85 відсотків шлаку відповідно. Суміші в інших пропорціях зустрічаються у франкомовних країнах під такими назвами, як ciment portland de fer, ciment métallurgique mixte, ciment de haut fourneau та ciment de liatier au clinker. Властивості цих шлакопортландцементів загалом подібні до властивостей портландцементу, але вони мають нижчий вміст вапна і вищий вміст кремнезему та глинозему. Шлакопортландцементи з вищим вмістом шлаку мають підвищену стійкість до хімічних впливів.
Іншим типом шлаковмісного цементу є суперсульфатний цемент, що складається з гранульованого шлаку, змішаного з 10-15% випаленого гіпсу або ангідриту (природного безводного сульфату кальцію) і декількома відсотками портландцементу. Міцність суперсульфатного цементу подібна до міцності портландцементу, але він має підвищену стійкість до багатьох форм хімічного впливу. Пуццоланові цементи – це суміші портландцементу і пуццоланового матеріалу, який може бути як природним, так і штучним. Природні пуццолани – це переважно матеріали вулканічного походження, але включають деякі діатоміти. Штучні матеріали включають летючу золу, обпалені глини та сланці. Пуццолани – це матеріали, які самі по собі не є цементуючими, але містять кремнезем (і глинозем) в реакційноздатній формі, здатній з’єднуватися з вапном у присутності води, утворюючи сполуки з цементуючими властивостями. Суміші вапна і пуцолану все ще знаходять деяке застосування, але в основному були витіснені сучасним пуцолановим цементом. Гідратація фракції портландцементу вивільняє вапно, необхідне для з’єднання з пуццоланом.
Високоглиноземистий цемент
Високоглиноземистий цемент – це цемент, що швидко твердне, виготовлений шляхом плавлення при температурі від 1 500 до 1 600 °C (2 730 до 2 910 °F) суміші бокситів і вапняку в ревербераційній, електричній печі або в обертовій печі. Він також може бути виготовлений шляхом спікання при температурі близько 1250 °C (2280 °F). Придатні боксити містять від 50 до 60 відсотків глинозему, до 25 відсотків оксиду заліза, не більше 5 відсотків кремнезему і від 10 до 30 відсотків гідратаційної води. Вапняк повинен містити лише невелику кількість кремнезему і магнезії. Цемент містить 35-40% вапна, 40-50% глинозему, до 15% оксидів заліза і бажано не більше 6% кремнезему. Основною цементуючою речовиною є алюмінат кальцію (CaO • Al2O3).
Високоглиноземистий цемент набирає велику частку своєї граничної міцності протягом 24 годин і має високу стійкість до хімічних впливів. Він також може бути використаний у вогнетривкій футеровці печей. Біла форма цементу, що містить мінімальні пропорції оксиду заліза і кремнезему, має видатні вогнетривкі властивості.
Цементи, що розширюються і безусадочні
Розширювальні та безусадочні цементи трохи розширюються при гідратації, компенсуючи тим самим невелике стиснення, яке відбувається при першому висиханні свіжого бетону. Вперше цементи, що розширюються, були вироблені у Франції приблизно в 1945 році. Американський тип являє собою суміш портландцементу і розширювача, виготовленого шляхом клінкерування суміші крейди, бокситів і гіпсу.
Гіпсові штукатурки
Гіпсові штукатурки використовуються для оштукатурювання, виготовлення гіпсових плит і плит, а також як матеріал для облицювання підлог. Ці гіпсові цементи в основному виробляються шляхом нагрівання природного гіпсу (дигідрат сульфату кальцію, CaSO4 • 2H2O) і його зневоднення до отримання гемігідрату сульфату кальцію (CaSO4 • ½H2O) або безводного (безводного) сульфату кальцію. Як сировину також використовують гіпс і ангідрит, отримані як побічні продукти в хімічному виробництві.
Гемігідрат, відомий як паризький гіпс, схоплюється протягом декількох хвилин при змішуванні з водою; для будівельних цілей додається сповільнювач, як правило, кератин, білок. Безводні штукатурки на основі сульфату кальцію застигають повільніше, і часто для прискорення схоплювання додають іншу сульфатну сіль у невеликих кількостях. Штукатурка для підлоги, спочатку відома під німецькою назвою Estrich Gips, відноситься до безводного типу.
Випробування цементу

Випробування на міцність бетонної колони (Photo by Daniel Ackerman/wbur.org).
Різні випробування, яким повинен відповідати цемент, викладені в національних специфікаціях на цемент для контролю дрібнозернистості, міцності, часу схоплювання і міцності цементу. Ці випробування по черзі описані нижче.
Тонкість помелу
Тонкість помелу довгий час контролювали за допомогою ситових тестів, але зараз в основному використовуються більш складні методи. Найпоширеніший метод, який використовується як для контролю процесу помелу, так і для тестування готового цементу, вимірює площу поверхні на одиницю ваги цементу шляхом визначення швидкості проходження повітря через шар цементу. Інші методи залежать від вимірювання гранулометричного складу за швидкістю осідання цементу в гасі або шляхом елюювання (розділення) в повітряному потоці.
Стан схоплювання
Після застигання цемент не повинен зазнавати помітного розширення, яке могло б зруйнувати розчин або бетон. Ця властивість перевіряється шляхом кип’ятіння застиглого цементу у воді або під дією пари під високим тиском. Неміцність може виникнути через наявність в цементі занадто великої кількості вільної магнезії або сильно обпаленого вільного вапна.
Час схоплювання
Схоплювання і твердіння цементу є безперервним процесом, але для цілей тестування виділяють два моменти. Початковий час схоплювання – це проміжок часу між змішуванням цементу з водою і часом, коли суміш втратила пластичність, ставши до певної міри жорсткою. Він позначає приблизно кінець періоду, коли вологій суміші можна надавати форму. Остаточний час схоплювання – це момент, коли затверділий цемент набуває достатньої міцності, щоб протистояти певному визначеному тиску. Більшість специфікацій вимагають, щоб початковий мінімальний час схоплювання при звичайних температурах становив близько 45 хвилин, а остаточний час схоплювання не перевищував 10-12 годин.
Міцність
Випробування, які вимірюють швидкість, з якою цемент набирає міцність, зазвичай проводяться на розчині, що зазвичай складається з однієї частини цементу і трьох частин піску, змішаних з певною кількістю води. Раніше використовувалися випробування на розтягнення брикетів, що мають форму вісімки, потовщеної в центрі, але вони були замінені або доповнені випробуваннями на стиск кубічних зразків або поперечними випробуваннями на призмах. Специфікація Американського товариства з випробувань матеріалів (ASTM) вимагає проведення випробувань на розтягнення на цементно-піщаному розчині у співвідношенні 1:3 і на стиск на розчині у співвідношенні 1:2,75. Британський інститут стандартів (BSI) пропонує в якості альтернативи випробування на стиск розчину у співвідношенні 1:3 або бетонного зразка. Міжнародний метод, виданий Міжнародною організацією зі стандартизації (ISO), вимагає проведення поперечного випробування призми з цементно-піщаного розчину у співвідношенні 1:3, а потім випробування на стиск двох половинок призми, що залишилися після її розлому при згинанні. Багато європейських країн прийняли цей метод. У всіх цих випробуваннях вказується гранулометричний склад піску і, як правило, його джерело.
У випробуваннях більшості цементів вказується мінімальна міцність через 3 і 7 днів, а іноді і через 28 днів, але для швидкотверднучого портландцементу іноді вимагається також випробування через 1 день. Для високоглиноземистого цементу потрібні випробування через 1 і 3 доби.
Вимоги до міцності, встановлені в різних країнах, не можна безпосередньо порівнювати через відмінності в методах випробувань. У реальному будівництві для перевірки міцності бетону проводять випробування на стиск циліндрів або кубів, виготовлених з бетону, що укладається.